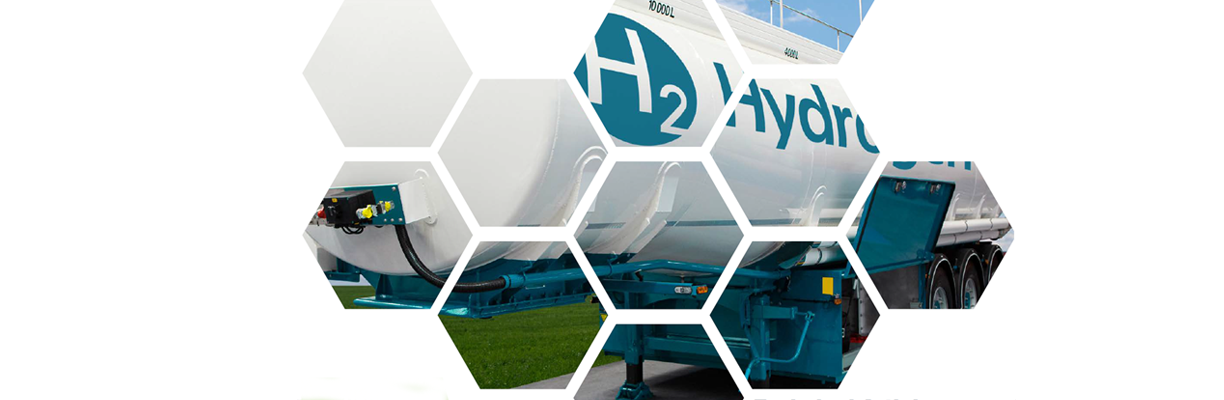
Leading the way in hazardous area static control
Hydrogen Safety: the importance of controlling static electricity
Countries around the world have set the strategic objective of reaching net-zero as soon as possible. One of the key enablers is the rapid development of the hydrogen economy. Vast amounts of public and private money are being invested in the production, storage and transportation of hydrogen as well as the fuelling station network for the increasing range of hydrogen vehicles.
As the hydrogen economy rapidly develops, safety must be the top priority. Standardisation is a key step on this journey to net-zero. The ISO 19880-1:2020 Standard is very specific about the requirements for grounding and bonding, including for hydrogen delivery systems such as trucks or trailers. The Standard states that electrical resistance between metallic parts connected or in contact together should be less than 10 ohms.
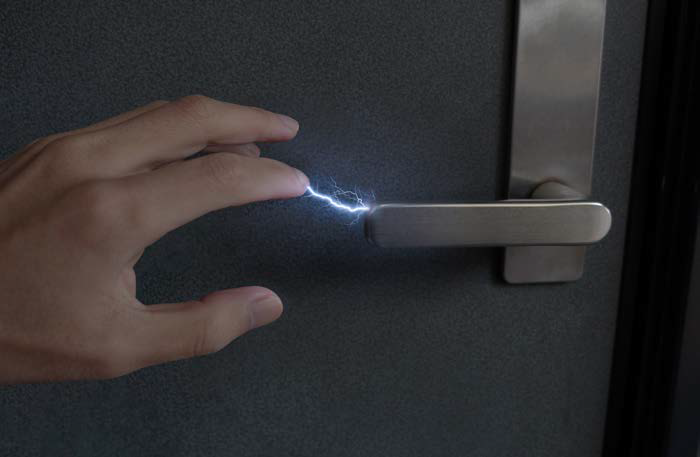
Static Electricity as an Ignition Source
Each day there are fires and explosions caused by the ignition of flammable and combustible chemicals. One of the most common causes of the ignition is a spark caused by a sudden discharge of accumulated static electricity.
When two differing materials move against each other, electrons can be exchanged, leaving an excess of positive charge on one material and an equal negative charge on the other. This is the generation of static electricity. During the transfer or processing of a material, significant amounts of static charge can accumulate very quickly, leading to the rapid increase of voltage on the object (e.g. road tanker).
Voltages can rapidly exceed the break-down voltage of the surrounding atmosphere and create the risk of a sudden discharge to a nearby conductor in the form of a spark.
The amount of energy released by this sudden discharge can easily exceed the Minimum Ignition Energy (MIE) of the potentially flammable atmosphere and thereby lead to a fire or explosion.
Newson Gale exists to design and manufacture solutions to mitigate against this risk.
The most effective way of avoiding a sudden static discharge is to ensure the object is grounded before and during the process by providing a low resistance path to true ground so that static electricity does not accumulate.
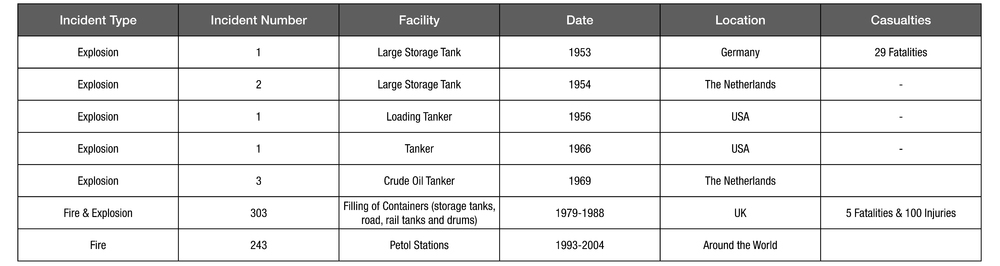
Table 1, Summary of static ignition incidents (Source: “An overview on static electricity”, Disaster Prevention and Management: An International Journal, (2008))
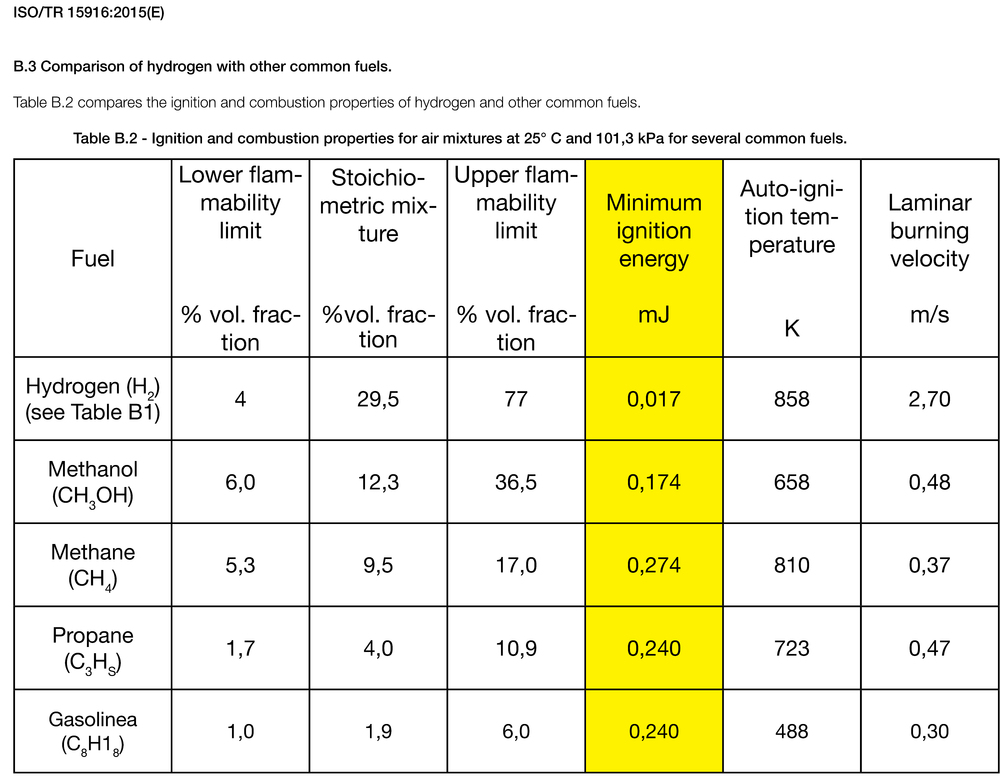
The Specific Properties of Hydrogen
The reason that controlling static electricity is so important for hydrogen safety is that the MIE is only a fraction of that of other fuels. This is highlighted in the following table taken from the ISO Technical Report ISO / TR 15916 ‘Basic considerations for the safety of hydrogen systems’.
The very small amount of energy required to ignite hydrogen means that it is classified within Gas Group IIC (Gas Group B in the US). Newson Gale’s Earth-Rite® II RTR is dedicated to grounding road tankers and large vehicles. It is certified to be installed and used in IIC environments, unlike many alternative systems.
The ease with which hydrogen can be ignited was outlined by S Tretsiakova-McNally, Ulster University, in ‘Lecture: sources of hydrogen ignition and prevention measures’
(Page 10):
“Thus, whilst electrostatic charging of those who refuel their vehicles with petrol rarely gives rise to ignitions, it is significant that the voltage required for hydrogen to be ignited is below 2kV. This voltage can be generated easily on people, without them being aware of it, standing on an insulating surface, so there is a potential for personnel to ignite hydrogen leaks very easily, without any apparent ignition source being present.”
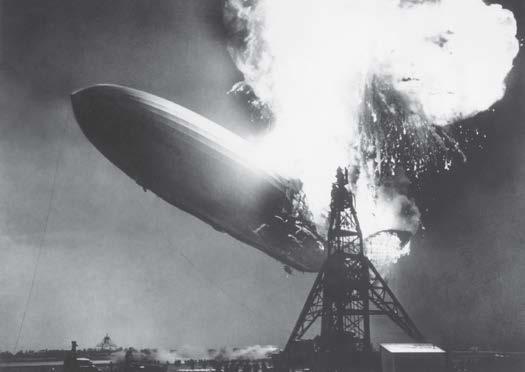
The most famous incident involving the ignition of hydrogen is the 1937 Hindenburg airship disaster. This massive airship was filled with hydrogen and became engulfed in flames, causing 36 fatalities. According to Konstantinos Giapis, Professor of Chemical Engineering at Caltech, the ignition was caused by sparks as static electricity discharged.
In the article, ‘Statistical analysis of fires and explosions attributed to static electricity over the last 50 years in Japanese industry’, Ohsawa found that 9% of such incidents involved hydrogen.
The ISO Technical Report on hydrogen safety clearly recognises a high-energy spark discharge as a major risk (5.3.7) and refers the reader to the recommended practices for grounding methods that can be found in various national and international standards (7.3.3.1).
Legislation concerning static electricity in hazardous atmospheres
The ignition risk posed by static electricity is addressed in European and North American legislation.
In Europe, Annex II of the ATEX Directive 2014/34/EU within Section 1.3.2 states: “Hazards arising from static electricity: Electrostatic charges capable of resulting in dangerous discharges must be prevented by means of appropriate measures”.
In the US, the Code of Federal Regulations that addresses hazardous location activities, 29 CFR Part 1910 Occupational Safety and Health Standards, states that “All ignition sources potentially present in flammable atmospheres, including static electricity, shall be mitigated or controlled”.
Section 10.12 of Canada’s Occupational Health and Safety Regulations (SOR/86-304) states that if a substance is flammable and static electricity is a potential ignition source that the employer “shall implement the standards set out in the United States National Fire Protection Association, Inc. publication NFPA 77, Recommended Practice on Static Electricity.”
Industry Codes of Practice
NFPA 77, Recommended Practice on Static Electricity is one of a number of industry codes of practice that addresses the ignition hazards of static electricity. In recognition of the ignition risks posed by static electricity these publications are produced and edited by committees of technical experts that participate in the hazardous process industries.
The publications in the table below are dedicated to helping QHSE professionals and plant engineers identify and control electrostatic ignition sources.
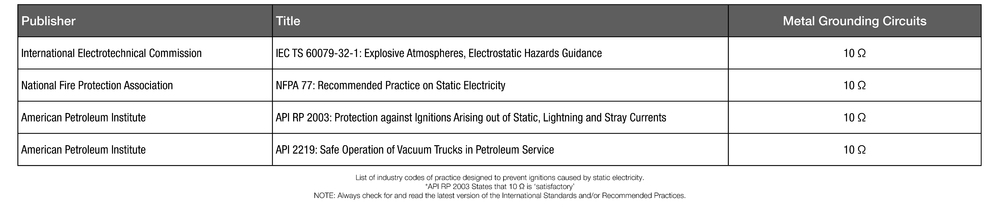
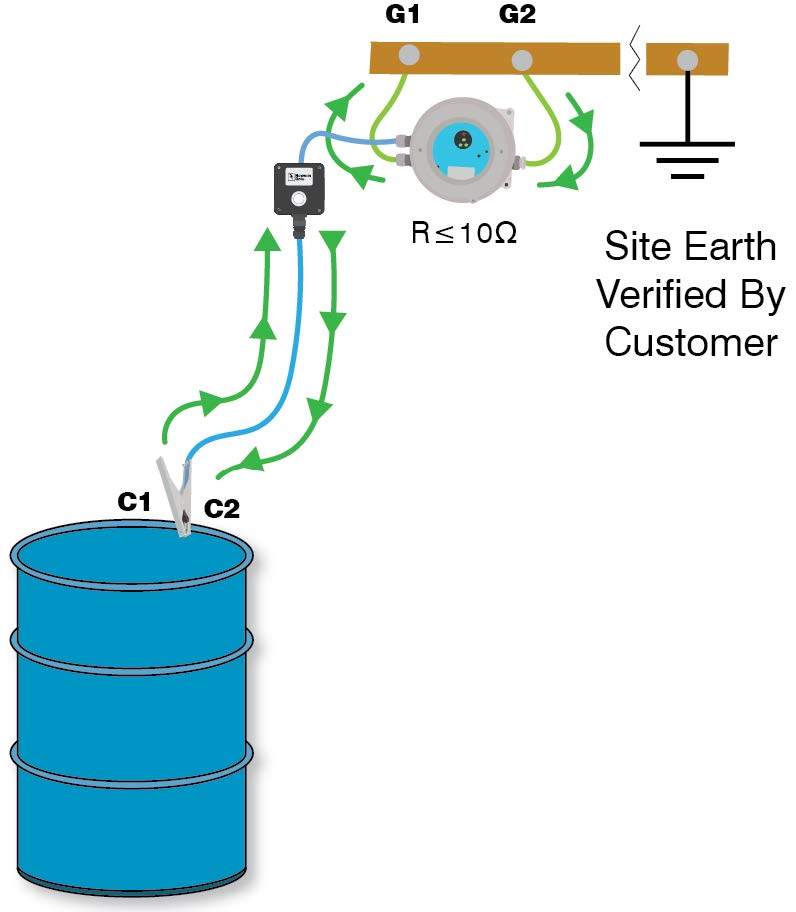
Target ≤ 10 ohms
Due to the harsh industrial environments in which grounding equipment typically operates, and because most grounding applications require many repeated connections and disconnections to process equipment, the robustness and reliability of the grounding solution is the primary concern with respect to intended performance. For that reason, best practice guidance such as IEC TS 60079-32-1 and NFPA 77 recommend resistance levels of 10 ohms or less between the object requiring static grounding and the verified
grounding point. The reason for this is that resistances higher than 10 ohms in the circuit between the object and the verified grounding point could indicate potential compromise of the grounding circuit, like a poor initial connection to the equipment via the grounding clamp, or loose / corroding connections that could otherwise prevent the passage of static charges to ground.
The most practical way to verify a resistance level of 10 ohms or less between the object to be grounded and the verified grounding point during the process is to use a monitored grounding system. A grounding system that continually monitors to a 10 ohm or less permissive threshold provides continuous indication of a connection that adheres to international standards and best practice recommendations.
Newson Gale’s Earth-Rite® II range of monitored grounding systems have achieved third-party verification (SIRA / CSA) of the 10 ohms or less permissive resistance threshold helping achieve compliance with international standards and best practice recommendations. Newson Gale is not aware of any other supplier having obtained a similar certificate confirming the 10 ohms or less performance.
International Standard
ISO 19880-1:2020 Gaseous hydrogen – Fuelling Stations
This Standard, dated March 2020, defines the minimum design requirements for the safety of all hydrogen fuelling stations. It covers fuelling stations for the following vehicles:
- Motorcycle
- Fork-lift truck
- Car
- Bus
- Truck
- Tram
- Train
The scope of the Standard also includes hydrogen delivery systems such as trucks or trailers. Mobile fuelling stations are also covered.
The Standard includes a section addressing the need to
mitigate the risk from static electricity.
10.2.3 Protection from ignition due to the accumulation of static charge
This section of the ISO 19880-1:2020 Standard is very specific about the requirements for grounding and bonding. Fortunately, Newson Gale’s products meet all of the requirements.
“Hydrogen systems shall be equipotentially bonded and grounded to prevent build-up of electrostatic charge … Electrical continuity should be ensured throughout the hydrogen system … The electrical resistance between metallic parts connected or in contact together should be less than 10 ohms.”
As discussed before, the Newson Gale Earth-Rite® II range of grounding systems continually monitor the connection resistance to a 10 ohms or less permissive threshold, and this has been verified by a third-party testing house.
“All hydrogen delivery vehicles shall be equipotentially bonded to the fixed storage hardware prior to flexible hose connection.”
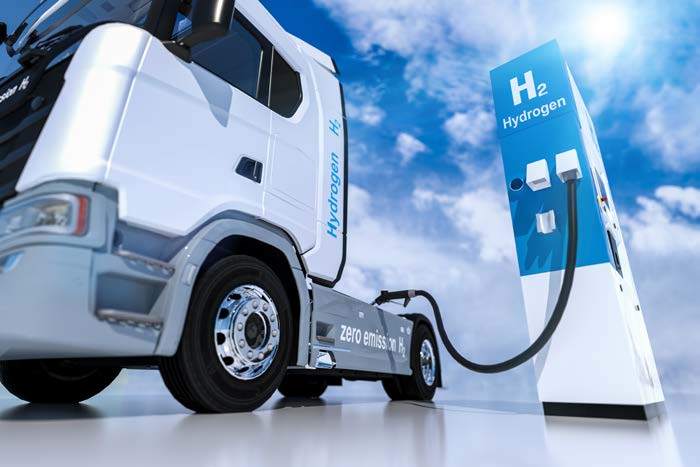
The Newson Gale Earth-Rite® II RTR verifies that it has been connected to an object with a capacitance typical of a large vehicle. This can mitigate against the risk of noncompliance with the Standard Operating Procedure.
This function of the Earth-Rite® II RTR also makes it the ideal product for the grounding of a large vehicle such as a truck or bus while it is being refuelled.
“The bonded hydrogen systems shall be grounded. The grounding system resistance shall be less than 1 megohm from any part within the hydrogen system.”
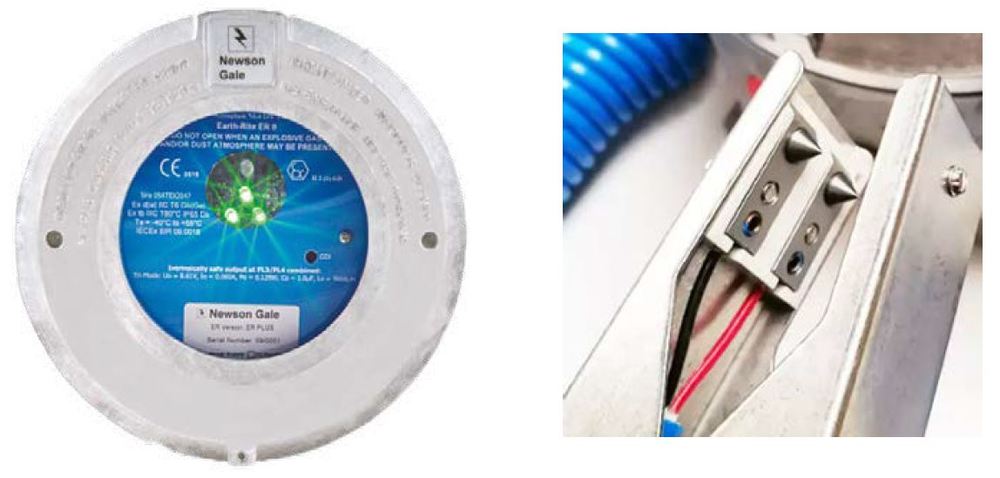
The Newson Gale Earth-Rite® II RTR and MGV grounding systems verify that the true ground resistance is less than approximately 1000 ohms.
“Grounding devices should be clearly visible or be essential to the correct functioning of the fuelling station, so that any shortcomings are quickly detected.”
If all of the parameter checks confirm permitted levels, the Newson Gale Earth-Rite® II grounding system will give clear visual indication of the ‘GO’ condition from three high-intensity flashing green LEDs. If any of the checks fails to confirm a permitted level, a solid red LED indicates the ‘NO-GO’ condition.
The Earth-Rite® II RTR also has the capability to be interlooked with the process so the flow of hydrogen in conjunction with the process control system can be controlled as per the ‘GO / NO-GO’ condition.
“Grounding devices should be robust and so installed that they are not affected by high resistance contamination, for example, by corrosion products or paint.”
Newson Gale pioneered the use of solid tungsten carbide teeth in grounding clamps. These very hard and very sharp teeth ensure a metal-to-metal contact with a bite that is
capable of penetrating through corrosion or paint.
As already outlined, Newson Gale’s range of static grounding systems help achieve compliance with the requirements of the new hydrogen ISO 19880-1:2020
Standard. There are also other reasons why companies that handle hazardous materials choose Newson Gale:
- Newson Gale has built a reputation for designing and manufacturing the most reliable static grounding systems on the market today.
- Over the last 40 years, Newson Gale has supplied tens of thousands of systems globally to protect people and plant from the ignition hazards of static electricity.
- Newson Gale systems have achieved global certification, so you can standardise your specification at various locations (see below).
- A global distribution network means that all your locations can access Newson Gale’s market-leading products.
- Our CompEx trained technical department and sales engineers are available online or onsite anywhere to demonstrate products and to tailor solutions to each application.
- With the broadest range of products in the market, Newson Gale has a solution for many applications and budgets.
Vil du vite mer om jording eller legge inn en bestilling?
Fyll ut personopplysningene dine så kontakter vi deg så fort som mulig.